Field-Proven Products to Optimize Horizontal Directional Drilling & Infrastructure Construction Projects
Di-Corp has developed a reputation for providing excellent HDD products and technical advice that exceed the expectations of directional drillers across Canada and the globe.
Meeting the Needs of HDD & Infrastructure Companies
Home » Horizontal Directional Drilling
Horizontal Directional Drilling
Di-Corp prides itself on our extensive supply offerings for the horizontal directional drilling market. We offer a full line-up of drilling fluids, drill rod greases, bentonites, cements, grouts, and soil solidification reagents. We are here to support you with the experienced technical field advice you need to deliver on all of your HDD project requirements.
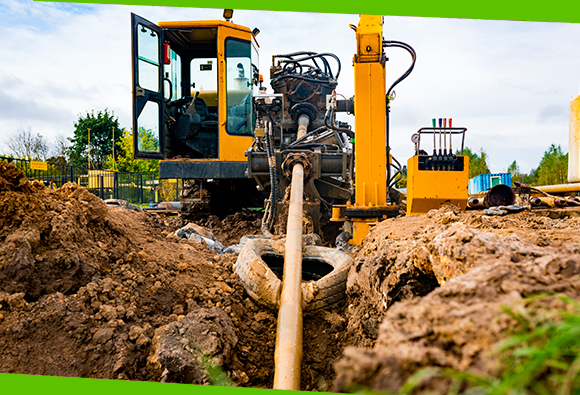
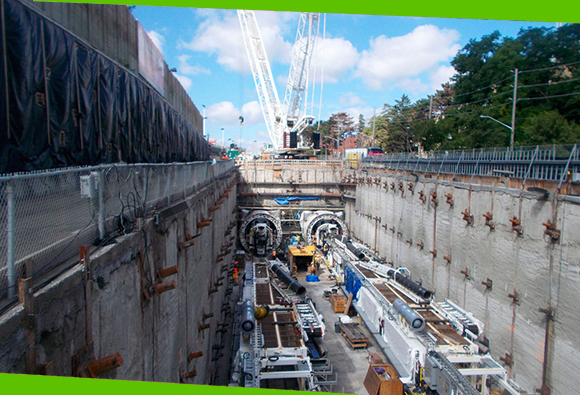
Infrastructure Construction
Di-Corp caters to various disciplines within the infrastructure marketplace. We have products and service expertise to help you with tailings pond and stormwater pond management, dams, tunneling, micro-tunneling, foundations, draining and pipelines, jet grouting and civil construction. We supply steel & bentonite products for virtually any form of drilling or construction application.
Why Choose Di-Corp?
A Full Range of
1000+ Products
Unmatched
Reliability & Quality
A Wealth of
Industry Knowledge
A Full Range of Premium Drilling Supplies & Products
HDD Drilling Fluids & Additives
Infrastructure Drilling Fluids & Additives
Steel Casing
Split Steel Casing
- ABOUT US
Drilling Fluids Service, Education, Engineering & Support
In addition to offering a full range of drilling fluids and additives, Di-Corp also offers an innovative approach to drilling fluids supply to help you get the most out of your dollars spent. Whether you need a technical consultation to help design a fluids program for your unique conditions, mud training or a dedicated mud school course for your drillers and drillers’ assistants, or just occasional troubleshooting to optimize your drilling fluids performance for a specific drill, Di-Corp’s service-oriented approach includes:
- Education for your front-line team.
- Engineering field-level tools to increase efficiency & performance.
- Support 24 hours a day, 365 days a year for urgent drilling fluids matters.
Serving the HDD & Infrastructure Industries Across the Globe
LOCATIONS
Serving the HDD & Infrastructure Industries Across the Globe
Frequently Asked Questions
Drilling fluid, also commonly called "mud" or "slurry," is a mixture of water and additives that is used to make the horizontal directional drilling process easier. The most common additives, which usually only account for around 3% of the mixture, are bentonite and polymer — sometimes a combination of the two, depending on the ground conditions. Bentonite is a type of clay that can be ground, refined and mixed with water to make a mud-like fluid used in the drilling process, hence the term "mud."
Proper HDD drilling fluid must be mixed correctly for the type of soil a bore will encounter. Di-Corp offers a wide range of bentonites and polymers for all ground conditions and project parameters. We also are happy to share our knowledge and expertise by offering to bring our "mud school" courses to your location, offering fluids mixing and mud testing training for your team.
Of course, every order can have different delivery parameters. But to ensure reliable, quick delivery, Di-Corp blends and packages many of its own proprietary Earth Pro brand drilling fluid additives and maintains a significant stock of key drilling mud ingredients such as bentonite and barite.
Our extensive international supply chain ensures that we always have a supply of raw materials ready to feed our blending and packaging facility in Edmonton, Alberta, Canada. In addition, we have a network of Di-Corp and third-party warehouses across Canada, plus key shipping partners and a network of nine distributors worldwide to help ensure our product is always readily available.
Earth Pro Mud Terminator can help you turn slurry into soil in minutes. It is a granular solidifying agent, a blend of super-absorbent polymer derived from 100-percent food-grade ingredients & accepted at landfills.
- CONTACT US
Request a Quote Today
Fill out the form below to request a quote for any of our products or to learn more about how Di-Corp’s products can help you maximize the production of your HDD or infrastructure business.
"*" indicates required fields